The ASTM A106 specification plays a crucial role in the construction of various critical infrastructures such as oil and gas refineries, power plants, petrochemical plants, boilers, and ships. This specification, specifically designed for carbon steel pipes, ensures the safe transportation of fluids and gases at elevated temperatures and pressure levels. It has three grades: Grade A, B, and C. ASTM A106 Grade B pipe is the standard specification for seamless carbon steel pipe for high-temperature service. The material is known for its excellent performance in high temperature, high pressure applications, with superior resistance to mechanical stress and corrosion. Furthermore, it exhibits great weldability, allowing for a wide range of applications in different industries.
Chemical composition of ASTM A106
The exact chemical composition of ASTM A106 varies slightly depending on the grade, but the primary elements are generally carbon, manganese, phosphorus, sulfur, and silicon.
Carbon is the principal hardening element and contributes significantly to the material’s strength and toughness.
Manganese enhances the steel’s hardness and strength while also improving its ductility and toughness.
Phosphorus and sulfur are typically kept at lower levels due to their potential negative impact on the material’s toughness and weldability.
Silicon is added to improve the steel’s strength, elasticity, and resistance to wear and heat.
However, it’s important to note that the exact amounts of these elements can vary depending on the specific grade of ASTM A106 being considered.
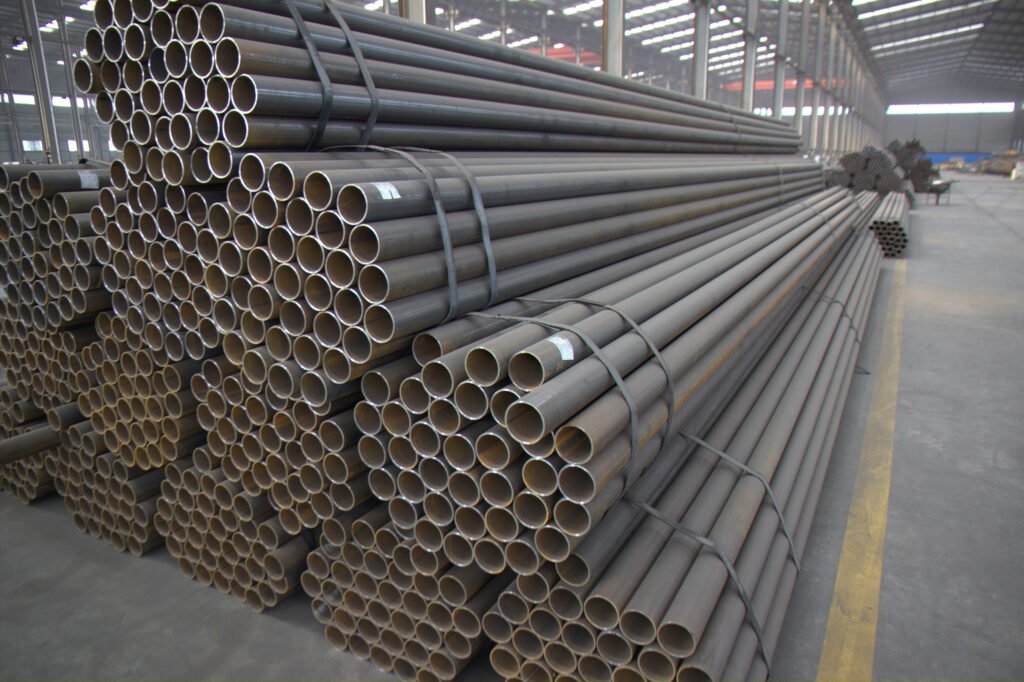
Mechanical Properties of ASTM A106
The mechanical properties of ASTM A106 make it a preferred choice for high temperature, high pressure applications. These properties include tensile strength, yield strength, and elongation. Tensile strength refers to the maximum amount of stress that ASTM A106 can endure before breaking or failing, which is quite high, making it suitable for high-stress environments. Yield strength is the stress at which ASTM A106 begins to deform plastically, meaning that it will not return to its original shape after the removal of the stress. Like its tensile strength, the yield strength of ASTM A106 is also quite high. Elongation measures the ability of ASTM A106 to stretch without breaking, enhancing its toughness and resilience. The extent of elongation is generally indicated as a percentage of the original length. These mechanical properties, coupled with its excellent resistance to wear, heat, and corrosion, make ASTM A106 a robust and versatile material suitable for various industrial applications.
Manufacturing Process of ASTM A106 Pipe
The manufacturing process of ASTM A106 pipes begins with the selection of the raw materials, typically a blend of carbon, manganese, phosphorus, sulfur, and silicon. These elements are then melted together in a furnace at high temperatures to create molten steel. The molten steel is then poured into casting molds to form billets, which are solid, square-shaped blocks of steel. These billets are then heated and elongated using a series of rollers in a process known as hot rolling. The heated, elongated billets are then shaped into a hollow tube through a procedure called extrusion or piercing. After the tube’s formation, it undergoes a process known as cold drawing or hot finished processing to refine its dimensions and improve its mechanical properties. The pipe is then subjected to heat treatment to relieve any stresses introduced during the manufacturing process and to enhance its hardness and strength. Finally, the pipe is tested for quality, including checks for dimensional accuracy, mechanical properties, and chemical composition, before being packaged and shipped. It’s important to note that the exact manufacturing process can vary depending on the specific grade of ASTM A106 being produced.
Advantages of ASTM A106
ASTM A106 offers several significant advantages that make it a preferred choice in various industrial applications. First and foremost, its ability to withstand high temperatures and pressures makes it ideal for high-stress environments. This capacity is especially beneficial in industries such as oil, gas, and power generation, where materials are often subjected to extreme conditions.
Furthermore, ASTM A106 exhibits excellent resistance to wear, heat, and corrosion, which contributes to its durability and long lifespan, reducing the need for frequent replacement or maintenance. This characteristic can lead to substantial cost savings over the material’s lifecycle.
In addition, ASTM A106 is highly weldable, allowing for a wide range of applications and installation options. This weldability does not compromise its strength or toughness, making it an excellent choice for structures that require robust and durable connections.
Finally, the natural strength of ASTM A106, combined with its high tensile and yield strength, means that it can endure significant stress without deforming or breaking, providing safety and reliability in demanding applications. Its high elongation ability further enhances its toughness and resilience, allowing it to stretch without breaking under tension.
Limitations of ASTM A106
Despite its various advantages and extensive use in many industries, ASTM A106 does come with certain limitations. One primary limitation is its performance in extremely low temperatures. ASTM A106 has a lower Charpy impact value at low temperatures, which means it can become brittle and more susceptible to cracking or breaking.
Another limitation is associated with its chemical composition. Even though the levels of phosphorus and sulfur are typically kept low due to their potential impact on toughness and weldability, their presence can still lead to issues such as hot-shortness or sulfide stress cracking.
Lastly, although ASTM A106 exhibits excellent resistance to corrosion, its resistance is not absolute. In certain environments with specific types of corrosive elements, especially those involving hydrogen sulfide or other aggressive chemicals, ASTM A106 might face corrosion-related challenges. Therefore, it’s crucial to consider these factors while choosing ASTM A106 for specific applications.
Applications of ASTM A106
ASTM A106 finds wide-ranging applications in various industrial sectors due to its impressive mechanical properties and robustness. It is extensively used in the oil and gas industry for pipeline transportation systems, where the ability to withstand high pressures and temperatures is paramount. The material’s strength, durability, and corrosion resistance make it suitable for use in power generation plants, particularly in steam generation systems. ASTM A106 is also applied in the construction industry for structural purposes such as bridge and building infrastructure, owing to its high yield strength and weldability. In addition, it is commonly used in the automotive industry for manufacturing vehicle parts that require high strength and resistance to wear and heat. Furthermore, it is used in the shipbuilding industry for its excellent toughness and resilience, essential properties for withstanding the harsh marine environment. Lastly, ASTM A106 is also prevalent in the chemical industry for constructing vessels and pipes that transport aggressive chemicals, given its decent resistance to various types of corrosion. Nevertheless, the choice of ASTM A106 for any application should be based on a comprehensive evaluation of the working conditions and the material’s compatibility with the specific environmental factors.
Conclusion
In conclusion, ASTM A106 is a highly versatile and durable material that is widely used in various industries due to its excellent mechanical properties and resistance to high temperatures, pressure, stress, and corrosion. Its chemical composition, including the amount of carbon, manganese, phosphorus, sulfur, and silicon present, plays a crucial role in determining its performance and suitability for