The world around us is held together by structures that depend on certain elements for their stability. One such element is Spiral Submerged Arc Welding (SSAW) pipes, which play a crucial role in the construction industry, oil and gas industry, and many other sectors. But how are these pipes produced? Let’s explore the intricate process.
What is SSAW?
Firstly, it’s important to understand what SSAW is. SSAW stands for Spiral Submerged Arc Welding. It refers to a specific method of pipe production under which the steel strip coils are fed through a spiral pipeline. The technique involves welding on the inside and outside, creating a robust structure.
The Production Process
The production process of SSAW pipes involves several key steps:
1. Uncoiling: The first step in the process is uncoiling the steel strip. This strip is then flatted in a machine to achieve the desired width and thickness.
2. Flattening: After uncoiling, the strip is flattened to remove any curvature or unevenness. This is crucial for maintaining the quality of the final product.
3. Edge Milling: The edges of the strip are then milled to prepare them for welding. This step ensures a clean, smooth surface that enhances the quality of the weld.
4. Forming: Next, the flat strip is gradually formed into a spiral shape. This is done using advanced machinery that ensures precision and consistency.
5. Welding: Once the strip is spirally shaped, it is welded from the inside and outside using submerged arc welding. This form of welding uses a flux-coated electrode, which when melted in the arc, forms a gas shield and slag. The gas shield protects the weld from atmospheric contamination, while the slag protects the weld pool.
6. Cutting: After the welding process, the pipe is cut to the desired length. This is done using high-speed cutting tools to ensure accuracy.
7. Visual Inspection: Each pipe undergoes a thorough visual inspection to check for any defects or inconsistencies.
8. Hydrostatic Testing: The final step in the production process involves conducting a hydrostatic test. This test checks the pipe’s strength and leak resistance by filling it with water under high pressure.
Quality Assurance
The quality of SSAW pipes is highly dependent on the quality of the raw materials and the precision of each production step. Therefore, manufacturers follow strict quality control measures at each stage of the production process. They also conduct various tests, such as tensile strength tests, impact tests, and bend tests, to ensure the pipe meets all industry standards.
Conclusion
The production of SSAW pipes is a complex process that requires precision, advanced machinery, and high-quality raw materials. However, the result is a robust, durable product that plays an integral role in many industries. Understanding this process can help us appreciate the work that goes into creating the structures that power our world.
The next time you see a large construction project, an oil rig, or even your local water supply system, remember the intricate process behind the SSAW pipes that make it all possible.
#JSFITTINGS #RAYOUNG #STEELPIPE #FLANGE #STEELPIPE #MADEINCHINA #MANUFFACTURER #FACTORY #PIPEELBOW #PIPE REDUCER #INDUSTRYFLANGE
Email: admin@jsfittings.com
Whats App: 008618003119682
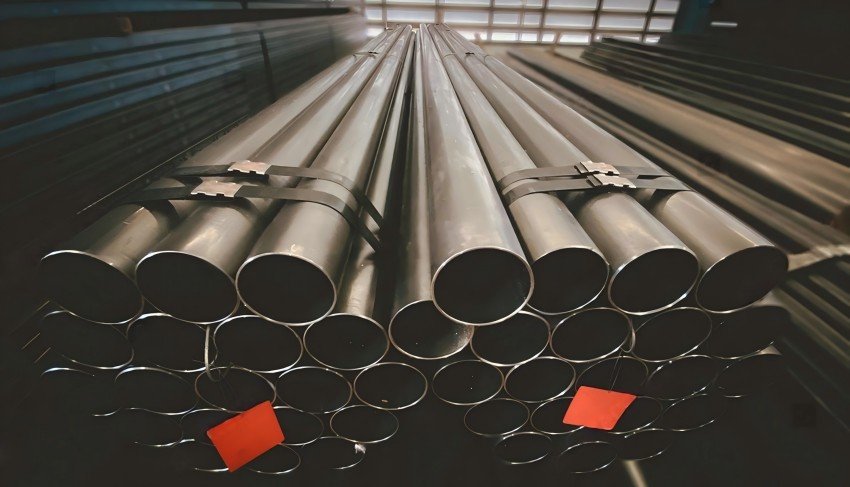